Why does your clay brick crack?
Author:Edith L Views:3772 Updatetime:April 07, 2022
Why does your clay brick crack?
The crack of the finished clay brick is a key factor influencing the product quality; in less severe cases, it may influence the quality grade evaluation of product; in severe cases, it may influence the users and is difficult to sell; in more severe cases, it may even cause a number of waste clay bricks and cause the unrecoverable economic losses to the clay brick plant owners.
Clay brick Cracks Caused by Raw Material
Clay brick Cracks Caused by Characteristics of Raw Material (clay)
1.Excessive Drying Sensitivity index
The drying sensitivity index is applied to measure the tendency scale of the product crack; the higher the drying sensitivity index is, the larger the tendency is to cause cracks on the products; on the contrary, the smaller the tendency is to cause cracks on the products. When the drying sensitivity index if more than 2, the cracks are almost inevitable; normally, the products don’t form cracks when the drying sensitivity index is less than 1. With the same drying sensitivity index, cracks seldom emerge for natural drying; however, it is difficult to control for artificial drying. The main reasons are that the time of artificial drying is short (normally 10-30 hours) and the time of natural drying is long (it is 20-40 times longer than the time of artificial drying). Thus, the natural drying is normal and it is difficult to control the cracks after artificial drying in some brick factories. This type of crack is most common in some clay brick factories and some brick factories with high mixing amount of clay.
Controlling Measures:
a.The raw materials to be applied shall be tested in advance before constructing the factory and the raw materials with high drying sensitivity index shall be applied with caution.
b.Add the proper amount of drying agent; slag, gangue, coal ash and iron-ore slag are all fine drying agents.
2.Poor Plasticity
The poor plasticity of the raw material will cause that molding is difficult; cracks are severe when molding; the ability of resisting cracks is poor due to the poor quality of green body and low mechanic strength even if molding is completed reluctantly, which is easy to occur cracks in the drying and baking process.
Controlling Measures:
a.The sandy clay is able to mix with plasticizers, such as bentonite, highly plastic clay and black liquor.
b.Gangue and shale, if you want to reduce the granularity and increase the plasticity, you can add plastic agent too.
3. Unreasonable particle Composition of Pug
The so-called grain composition indicates the proportions of particle with various sizes in the pug. Generally, three types of particles are required, namely fine powder (also called plastic particles, less than 0.053mm), filling particle (0.053-1.2㎜) and coarse aggregate (decoration particle, 1.2-2.4㎜). The content of fine powder determines the plasticity of pug, normally accounting for 30-50%; the filling particle shall account for 20-65%; the function of these particle is to keep the adobe bricks from excessive shrinkage, cracks and deformation; the coarse aggregate shall account for 0-30%; it may not be applied if coarse aggregate decoration is not needed.
Controlling Measures: Applying more than two types of the above-mentioned raw materials and adjusting the composition of grain size is able to guarantee reasonable grain composition.
clay bricks cracks Caused by Management
Unreasonable Manufacturing Technique (Mainly Uneven Mixing)
When the brick is manufactured with two types of raw materials or more , uneven mixing may cause clay bricks cracks for the drying and baking shrinkage of the two types of raw materials are exactly the same, which is easy to form the internal stress; the cracks are inevitable after drying and baking.
Controlling Measures:
Improve the process and manage to mix evenly. The raw materials had better be mixed according to the proportion before being put into the crushers. In this way, the mixing effect will be better after three mixing processes, namely crushing, screening and mixing. After two types of raw materials are crushed and screened separately and then are mixed in the mixer, the ideal effect is hardly to reach. Furthermore, the greater difference of the raw material proportion is, the poorer the mixing effect is and the higher possibility to emerge cracks is.
Inadequate Aging Conditions
Inadequate aging conditions, namely inadequate aging effect, may cause clay bricks cracks.
Aging is also called curing storage. The objective is to enable the moisture to penetrate sufficiently and the clay to relieve and loose evenly. The aging shall possess four conditions: granularity, moisture, time and temperature; each of the four conditions is not able to be omitted. The smaller the granularity is, the better the aging effect is; the moisture reaches the molding moisture is optimum when entering the brick raw material warehouse; the time shall be more than 72 hours; the temperature of the brick raw material warehouse had better be maintained more than 10℃ (the lower the temperature is, the longer the aging period is).
We possess such experience in manufacturing: the pug stored before maintenance with stopping production is able to be applied for reproduction next time. This is due to the extension of aging period; the same pug is better to apply in summer than in winter; the reason is that the temperature in summer is higher than that in winter.
Contact us for more information now!
Whatsapp/mobile: +86 18103842990
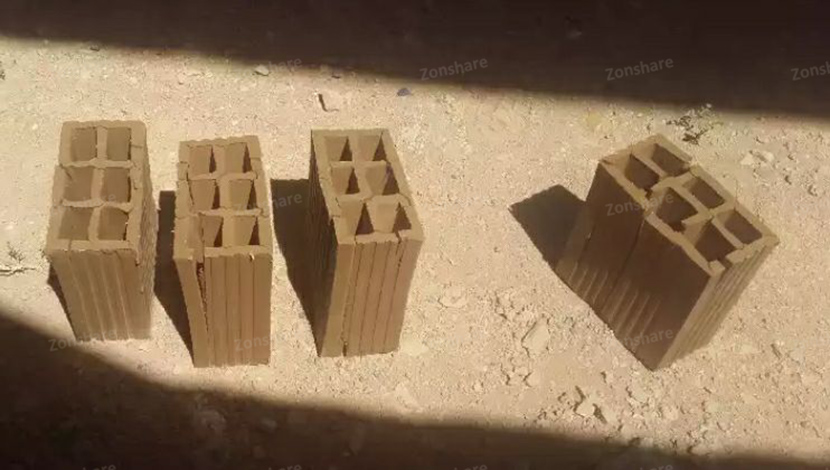
The crack of the finished clay brick is a key factor influencing the product quality; in less severe cases, it may influence the quality grade evaluation of product; in severe cases, it may influence the users and is difficult to sell; in more severe cases, it may even cause a number of waste clay bricks and cause the unrecoverable economic losses to the clay brick plant owners.
Clay brick Cracks Caused by Raw Material
Clay brick Cracks Caused by Characteristics of Raw Material (clay)
1.Excessive Drying Sensitivity index
The drying sensitivity index is applied to measure the tendency scale of the product crack; the higher the drying sensitivity index is, the larger the tendency is to cause cracks on the products; on the contrary, the smaller the tendency is to cause cracks on the products. When the drying sensitivity index if more than 2, the cracks are almost inevitable; normally, the products don’t form cracks when the drying sensitivity index is less than 1. With the same drying sensitivity index, cracks seldom emerge for natural drying; however, it is difficult to control for artificial drying. The main reasons are that the time of artificial drying is short (normally 10-30 hours) and the time of natural drying is long (it is 20-40 times longer than the time of artificial drying). Thus, the natural drying is normal and it is difficult to control the cracks after artificial drying in some brick factories. This type of crack is most common in some clay brick factories and some brick factories with high mixing amount of clay.
Controlling Measures:
a.The raw materials to be applied shall be tested in advance before constructing the factory and the raw materials with high drying sensitivity index shall be applied with caution.
b.Add the proper amount of drying agent; slag, gangue, coal ash and iron-ore slag are all fine drying agents.
2.Poor Plasticity
The poor plasticity of the raw material will cause that molding is difficult; cracks are severe when molding; the ability of resisting cracks is poor due to the poor quality of green body and low mechanic strength even if molding is completed reluctantly, which is easy to occur cracks in the drying and baking process.
Controlling Measures:
a.The sandy clay is able to mix with plasticizers, such as bentonite, highly plastic clay and black liquor.
b.Gangue and shale, if you want to reduce the granularity and increase the plasticity, you can add plastic agent too.
3. Unreasonable particle Composition of Pug
The so-called grain composition indicates the proportions of particle with various sizes in the pug. Generally, three types of particles are required, namely fine powder (also called plastic particles, less than 0.053mm), filling particle (0.053-1.2㎜) and coarse aggregate (decoration particle, 1.2-2.4㎜). The content of fine powder determines the plasticity of pug, normally accounting for 30-50%; the filling particle shall account for 20-65%; the function of these particle is to keep the adobe bricks from excessive shrinkage, cracks and deformation; the coarse aggregate shall account for 0-30%; it may not be applied if coarse aggregate decoration is not needed.
Controlling Measures: Applying more than two types of the above-mentioned raw materials and adjusting the composition of grain size is able to guarantee reasonable grain composition.
clay bricks cracks Caused by Management
Unreasonable Manufacturing Technique (Mainly Uneven Mixing)
When the brick is manufactured with two types of raw materials or more , uneven mixing may cause clay bricks cracks for the drying and baking shrinkage of the two types of raw materials are exactly the same, which is easy to form the internal stress; the cracks are inevitable after drying and baking.
Controlling Measures:
Improve the process and manage to mix evenly. The raw materials had better be mixed according to the proportion before being put into the crushers. In this way, the mixing effect will be better after three mixing processes, namely crushing, screening and mixing. After two types of raw materials are crushed and screened separately and then are mixed in the mixer, the ideal effect is hardly to reach. Furthermore, the greater difference of the raw material proportion is, the poorer the mixing effect is and the higher possibility to emerge cracks is.
Inadequate Aging Conditions
Inadequate aging conditions, namely inadequate aging effect, may cause clay bricks cracks.
Aging is also called curing storage. The objective is to enable the moisture to penetrate sufficiently and the clay to relieve and loose evenly. The aging shall possess four conditions: granularity, moisture, time and temperature; each of the four conditions is not able to be omitted. The smaller the granularity is, the better the aging effect is; the moisture reaches the molding moisture is optimum when entering the brick raw material warehouse; the time shall be more than 72 hours; the temperature of the brick raw material warehouse had better be maintained more than 10℃ (the lower the temperature is, the longer the aging period is).
We possess such experience in manufacturing: the pug stored before maintenance with stopping production is able to be applied for reproduction next time. This is due to the extension of aging period; the same pug is better to apply in summer than in winter; the reason is that the temperature in summer is higher than that in winter.
Contact us for more information now!
Whatsapp/mobile: +86 18103842990
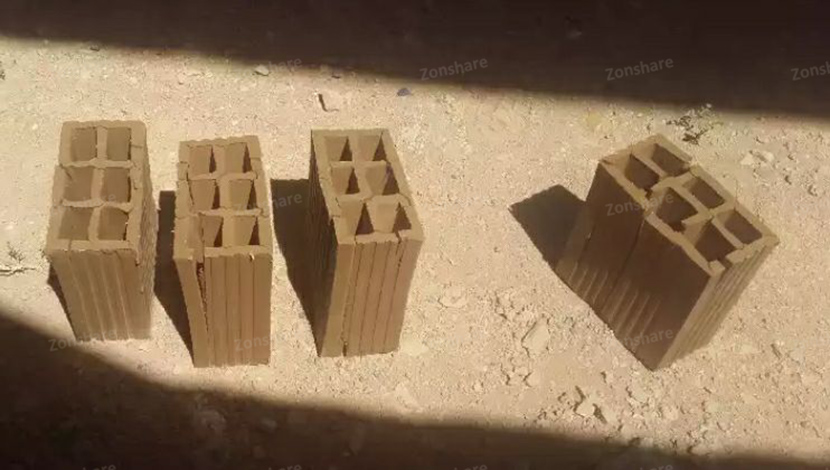